Process
Flexible packaging production is a combination of specialized processes and fine techniques performed by our technicians in various departments. With many years of experience, all our technicians have become masters who take pride in the quality of our final products. Our staff is trained to approach all projects with dedication to help the customer succeed.
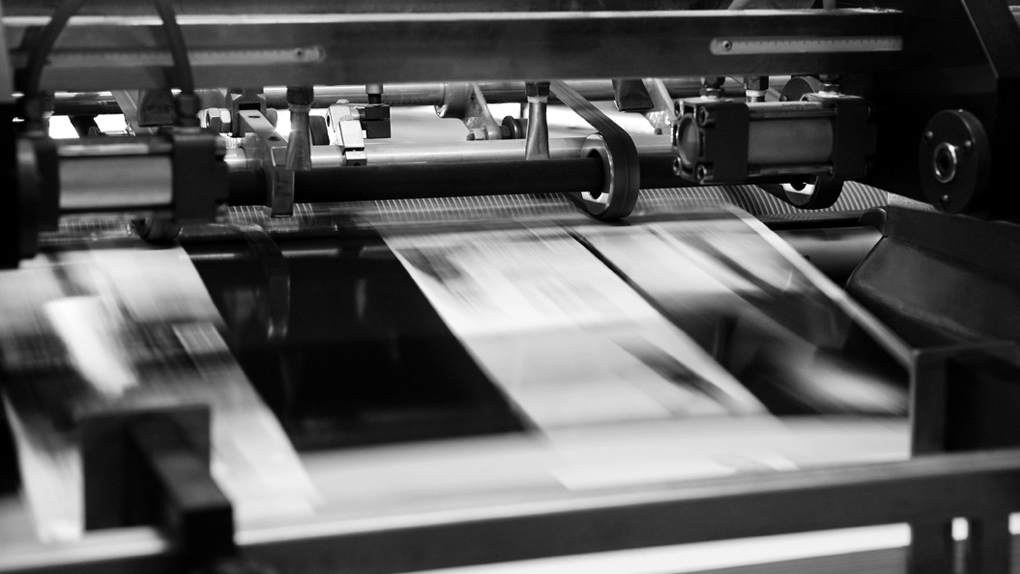
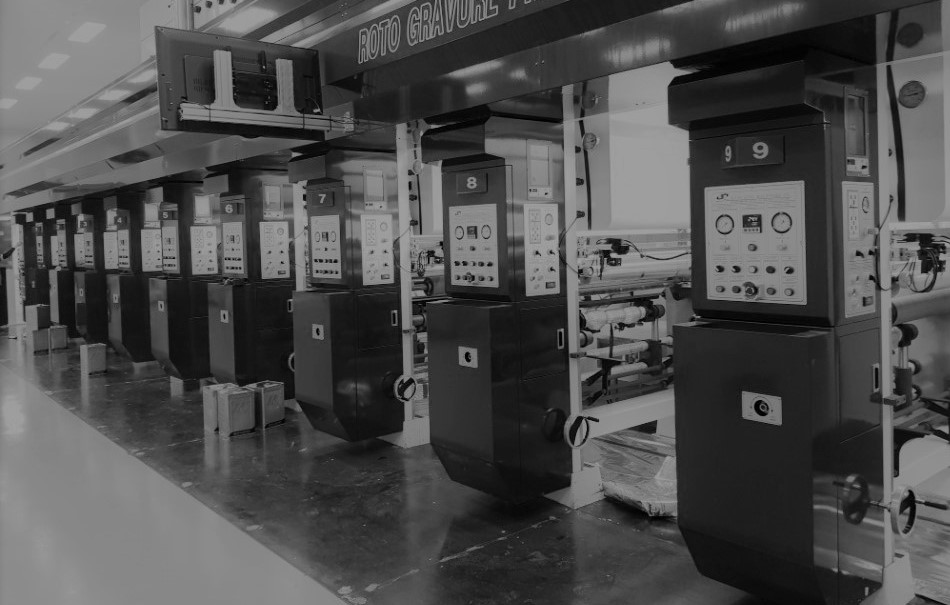
Rotogravure is the traditional printing method with metal plates and separate ink stations. It provides exceptionally crisp print quality, while accommodating higher quantity print runs.
Digital printing is the similar method to your conventional digital printer at home. Our specialized industrial grade digital printer is the perfect option for those looking for smaller quantity runs.
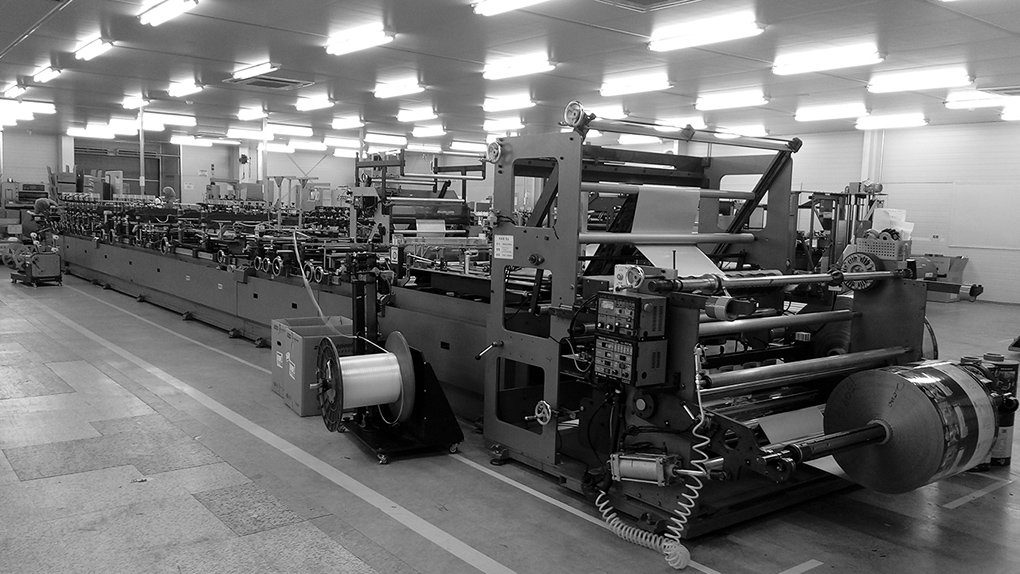
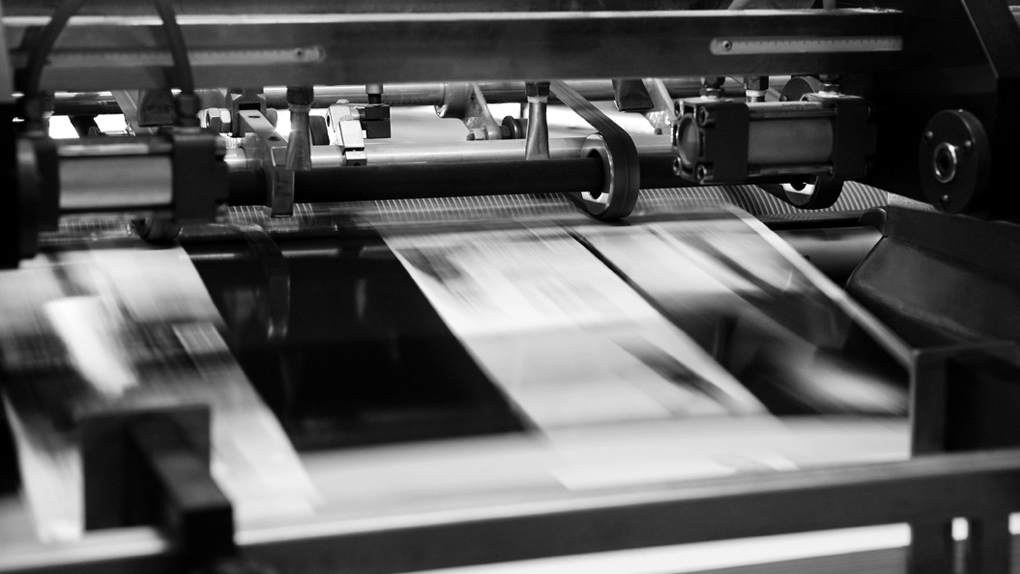
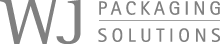
5355 Parkwood Place, Richmond, BC, V6V 2N1, Canada
tel. 604 303 5920 fax. 604 303 5922 email. info@wjpkg.com